載入中……
[供應]電爐H13圓棒
- 產(chǎn)品產(chǎn)地:進口/國產(chǎn)
- 產(chǎn)品品牌:博揚13580797772
- 包裝規(guī)格:H13
- 產(chǎn)品數(shù)量:28
- 計量單位:千克
- 產(chǎn)品單價:900000
- 更新日期:2018-07-11 15:44:57
- 有效期至:2019-07-11
-
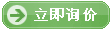
-
- 收藏此信息
電爐H13圓棒
詳細信息
【銷售熱線:李婷13129407666】【0769-81874568】【QQ:1783733346】
H13模具鋼
H13是熱作模具鋼,執(zhí)行標準GB/T1299—2000。統(tǒng)一數(shù)字代號T20502;牌號4Cr5MoSiV1;合金工具鋼簡稱合工鋼,是在碳工鋼的基礎上加入合金元素而形成的鋼種。其中合工鋼包括:量具刃具用鋼、耐沖擊工具用鋼、冷作模具鋼、熱作模具鋼、無磁模具鋼、塑料模具鋼。
 
化學成分
C0.32~0.45,
 
Si0.80~1.20,
 A
Mn0.20~0.50,
 
Cr4.75~5.50,
 
Mo1.10~1.75,
 
V0.80~1.20,
 
p≤0.030,
 
S≤0.030;
 
用途
H13模具鋼用于制造沖擊載荷大的鍛模,熱擠壓模,精鍛模;鋁、銅及其合金壓鑄模。
 
規(guī)格
H13模具鋼板寬度(210-610)*厚度(6-80)熱軋
 
H13模具鋼管外徑(6-219)*壁厚(0.5-25)
 
H13模具鋼錠電渣錠0.35T0.5T0.75T1.0T
 
1.5T
1.8T2.0T2.2T2.8T(3.0-8.0)T
 
熱處理
(交貨狀態(tài):布氏硬度HBW10/3000(小于等于235))
 
淬火:790度±15度預熱
 
1000度(鹽?。┗?010度(爐控氣氛)±6度加熱
 
保溫5~15min空冷
 
550度±6度回火退火、熱加工;
 
特性
電渣重容鋼,該鋼具有高的淬透性和抗熱裂能力,該鋼含有較高含量的碳和釩,耐磨性好,韌性相對有所減弱,具有良好的耐熱性,在較高溫度時具有較好的強度和硬度,高的耐磨性的韌性,優(yōu)良的綜合力學性能和較高的抗回火穩(wěn)定性。
 
硬度分析
鋼中含碳量決定淬火鋼的基體硬度,按鋼中含碳量與淬火鋼硬度的關系曲線可以知道,H13模具鋼淬火硬度在55HRC左右。對工具鋼而言,鋼中的碳一部分進入鋼的基體中引起固溶強化。另外一部分碳將和合金元素中的碳化物形成元素結(jié)合成合金碳化物。對熱作模具鋼,這種合金碳化物除少量殘留的以外,還要求它在回火過程中在淬火馬氏體基體上彌散析出產(chǎn)生兩次硬化現(xiàn)象。從而由均勻分布的殘留合金碳化合物和回火馬氏體的組織來決定熱作模具鋼的性能。由此可見,鋼中的含C量不能太低。
 
H13熱處理工藝
1.預先熱處理市場上供應的H13鋼鋼材和模坯,在鋼廠都已作好退火熱處理,保證了具有良好的金相組織,適當?shù)挠捕?,良好的加工性,無需再進行退火。但制造廠進行改鍛后破壞了原來的組織和性能,增加了鍛造應力,必須進行重新退火。
 
等溫球化退火工藝為:860~890℃加熱保溫2h,降溫到740~760℃等溫4h,爐冷到500℃左右出爐。
 
2.淬火及回火要求韌性好的模具淬火工藝規(guī)范:加熱溫度1020~1050℃,油冷或空冷,硬度54~58HRC;要求熱硬性為主的模具淬火工藝規(guī)范、加熱溫度1050~1080℃,油冷,硬度56~58HRC。
 
推薦回火溫度:530~560℃,硬度48~52HRC;回火溫度560~580℃;硬度47~49HRC。
 
回火應進行兩次。在500℃回火時,出現(xiàn)回火二次硬化峰,回火硬度最高,峰值在55HRC左右,但韌性最差。因此,回火工藝應避開500℃左右為宜。根據(jù)模具的使用需要,在540~620℃范圍內(nèi)回火較好。
 
淬火加熱應進行兩次預熱(600~650℃,800~850℃),以減少加熱過程產(chǎn)生熱應力。
 
3.化學熱處理H13鋼若進行氣體滲氮或氮碳共滲可使模具進一步強化,但其氮化溫度不應高于回火溫度,以保證心部強度不降低,從而提高模具的使用壽命。
 
H13模具鋼的化學成份
H13鋼是C-Cr-Mo-Si-V型鋼,在世界上的應用極其普遍,同時各國許多學者對它進行了廣泛的研究,并在探究化學成分的改進。鋼的應用廣泛和具有優(yōu)良的特性,主要由鋼的化學成分決定的。當然鋼中雜質(zhì)元素必須降低,有資料表明,當Rm在1550MPa時,材料含硫量由0.005%降到0.003%,會使沖擊韌度提高約13J。十分明顯,NADCA207-2003標準就規(guī)定:優(yōu)級(premium)H13鋼含硫量小于0.005%,而超級(superior)的應小于0.003%S和0.015%P。下面對H13鋼的成分加以分析。
 
碳:美國AISIH13,UNS
T20813,ASTM(最新版)的H13和FEDQQ-T-570的H13鋼的含碳量都規(guī)定為(0.32~0.45)%,是所有H13鋼中含碳量范圍最寬的。德國X40CrMoV5-1和1.2344的含碳量為(0.37~0.43)%,含碳量范圍較窄,德國DIN17350中還有X38CrMoV5-1的含碳量為(0.36~0.42)%。日本SKD61的含碳量為(0.32~0.42)%。我國GB/T1299和YB/T094中4Cr5MoSiV1和SM4Cr5MoSiV1的含碳量為(0.32~0.42)%和(0.32~0.45)%,分別與SKD61和AISIH13相同。特別要指出的是:北美壓鑄協(xié)會NADCA207-90、207-97和207-2003標準中對H13鋼的含碳量都規(guī)定為(0.37~0.42)%。
 
鋼中含碳量決定淬火鋼的基體硬度,按鋼中含碳量與淬火鋼硬度的關系曲線可以知道,H13鋼的淬火硬度在55HRC左右。對工具鋼而言,鋼中的碳一部分進入鋼的基體中引起固溶強化。另外一部分碳將和合金元素中的碳化物形成元素結(jié)合成合金碳化物。對熱作模具鋼,這種合金碳化物除少量殘留的以外,還要求它在回火過程中在淬火馬氏體基體上彌散析出產(chǎn)生兩次硬化現(xiàn)象。從而由均勻分布的殘留合金碳化合物和回火馬氏體的組織來決定熱作模具鋼的性能。由此可見,鋼中的含C量不能太低。
 
含5%Cr的H13鋼應具有高的韌度,故其含C量應保持在形成少量合金C化物的水平上。Woodyatt和Krauss指出在870℃的Fe-Cr-C三元相圖上,H13鋼的位置在奧氏體A和(A+M3C+M7C3)三相區(qū)的交界位置處較好。相應的含C量約0.4%。圖上還標出增加C或Cr量使M7C3量增多,具有更高耐磨性能的A2和D2鋼以作比較。另外重要的是,保持相對較低的含C量是使鋼的Ms點取于相對較高的溫度水平(H13鋼的Ms一般資料介紹為340℃左右),使該鋼在淬冷至室溫時獲得以馬氏體為主加少量殘余A和殘留均勻分布的合金C化物組織,并經(jīng)回火后獲得均勻的回火馬氏體組織。避免使過多殘余奧氏體在工作溫度下發(fā)生轉(zhuǎn)變影響工件的工作性能或變形。這些少量殘余奧氏體在淬火以后的兩次或三次回火過程中應予以轉(zhuǎn)變完全。這兒順便指出,H13鋼淬火后得到的馬氏體組織為板條M+少量片狀M+少量殘余A。經(jīng)回火后在板條狀M上析出的很細的合金碳化物,國內(nèi)學者也作了一定工作。
 
H13模具鋼分析
眾所周知,鋼中增加碳含量將提高鋼的強度,對熱作模具鋼而言,會使高溫強度、熱態(tài)硬度和耐磨損性提高,但會導致其韌度的降低。學者在工具鋼產(chǎn)品手冊文獻中將各類H型鋼的性能比較很明顯證明了這個觀點。通常認為導致鋼塑性和韌度降低的含碳量界限為0.4%。為此要求人們在鋼合金化設計時遵循下述原則:在保持強度前提下要盡可能降低鋼的含碳量,有資料已提出:在鋼抗拉強度達1550MPa以上時,含C量在0.3%-0.4%為宜。H13鋼的強度Rm,有文獻介紹為1503.1MPa(46HRC時)和1937.5MPa(51HRC時)。
 
查閱FORD和GM公司資料推薦的TQ-1、Dievar和ADC3等鋼中的含C量都為0.39%和0.38%等,相應的韌度指標等列于表1,其理由可由此管窺所及。
同類型其他產(chǎn)品
免責聲明:所展示的信息由企業(yè)自行提供,內(nèi)容的真實性、和合法性由發(fā)布企業(yè)負責,浙江民營企業(yè)網(wǎng)對此不承擔任何保證責任。
友情提醒:普通會員信息未經(jīng)我們?nèi)斯ふJ證,為了保障您的利益,建議優(yōu)先選擇浙商通會員。